Enhancing Quality Through Supplier Corrective Action Requests (SCARs)
- mcphersonqualityma
- Jul 3, 2024
- 2 min read
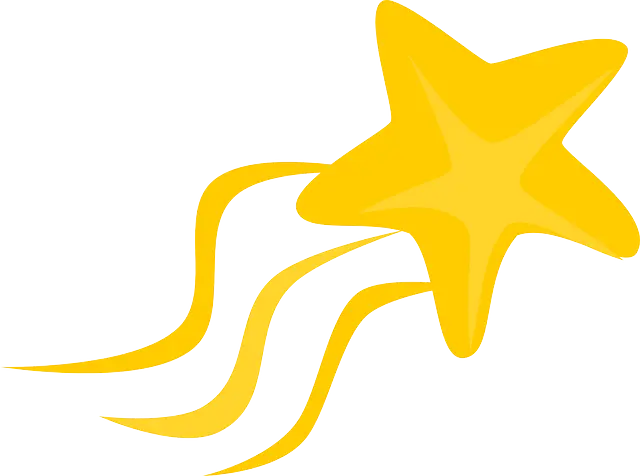
When aiming to elevate quality standards within an organization, the role of quality audits cannot be overstated. These audits are crucial for uncovering non-conformances that may arise internally, ensuring that processes and outputs meet stringent quality benchmarks. However, it's equally vital to extend this vigilance to external stakeholders, particularly suppliers.
Securing raw materials of optimal quality is paramount, as the old adage goes, "garbage in, garbage out." This underscores the importance of implementing Supplier Corrective Action Requests (SCARs) as a formal mechanism to address and rectify issues related to products or services supplied by external partners.
SCARs play a pivotal role in several key aspects:
Issue Resolution: They serve as a structured approach to report and resolve issues concerning the quality, performance, or compliance of supplied goods or services. By promptly addressing non-conformances and defects, organizations uphold product integrity and service excellence.

Quality Improvement: Through systematic documentation and corrective actions, SCARs facilitate continuous improvement in the quality of received products. This fosters reliability, consistency, and heightened customer satisfaction.
Supplier Performance Management: SCARs are integral to evaluating supplier performance over time. They provide valuable insights into supplier responsiveness, quality standards adherence, and overall reliability in meeting organizational expectations.
Prevention of Recurrence: Beyond addressing immediate issues, SCARs focus on root cause analysis and preventive measures. By identifying underlying causes and implementing robust corrective actions, organizations mitigate the risk of recurring issues.
Regulatory Compliance: In regulated industries, SCARs ensure adherence to stringent quality standards and regulatory requirements. They document how non-conformances are managed, demonstrating organizational commitment to compliance and accountability.
Communication and Documentation: SCARs serve as formal records of communication between organizations and their suppliers. They detail issue specifics, investigative findings, corrective actions taken, and outcomes, providing a transparent audit trail.
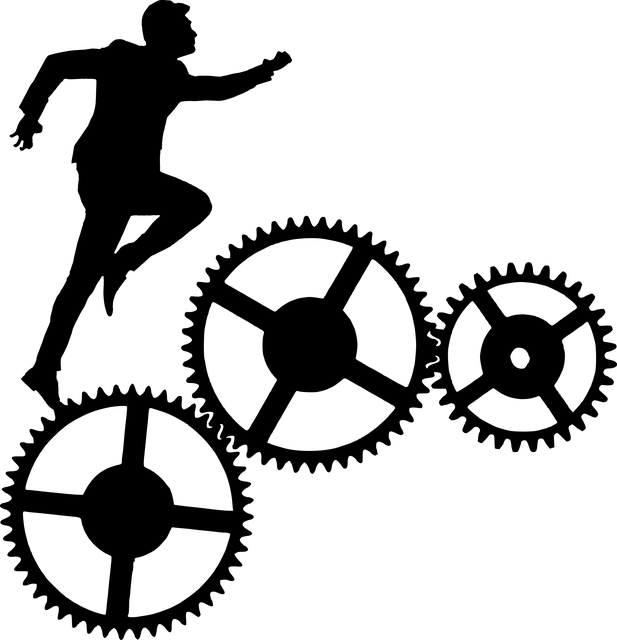
Continuous Improvement: Embracing SCARs fosters a culture of continuous improvement across the supply chain. By proactively addressing challenges and fostering collaborative problem-solving with suppliers, organizations drive sustained enhancements in product quality and supplier relationships.
In summary, SCARs represent a cornerstone in maintaining high-quality standards, effective supplier management, regulatory compliance, and fostering a culture of continual improvement. By leveraging SCARs diligently, organizations not only safeguard their reputation but also enhance operational excellence and customer satisfaction.
Kereen R. McPherson
CEO/Founder
KRMcPherson Quality Management (KQM)
LI: Ms Kereen McPherson
1-868-761-8206
コメント